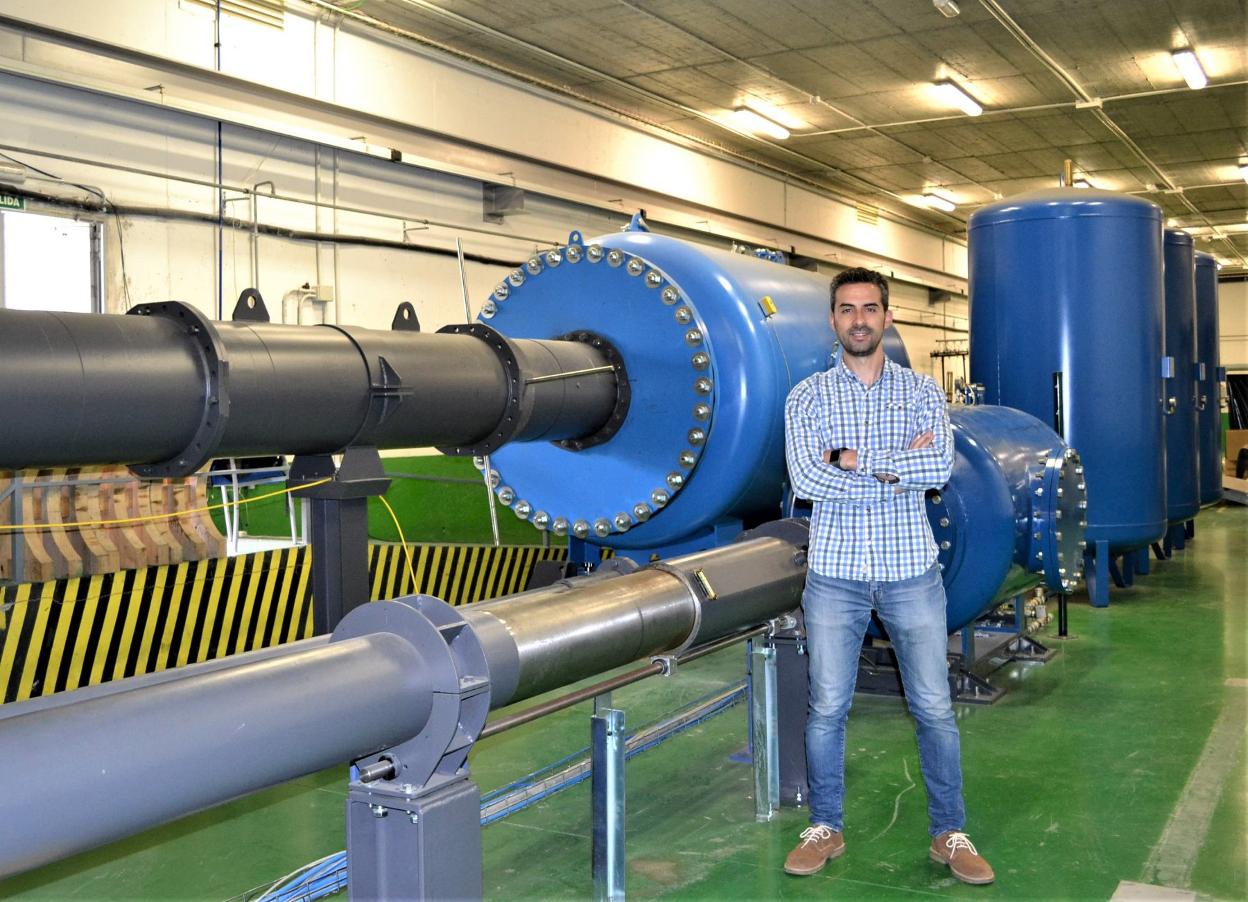
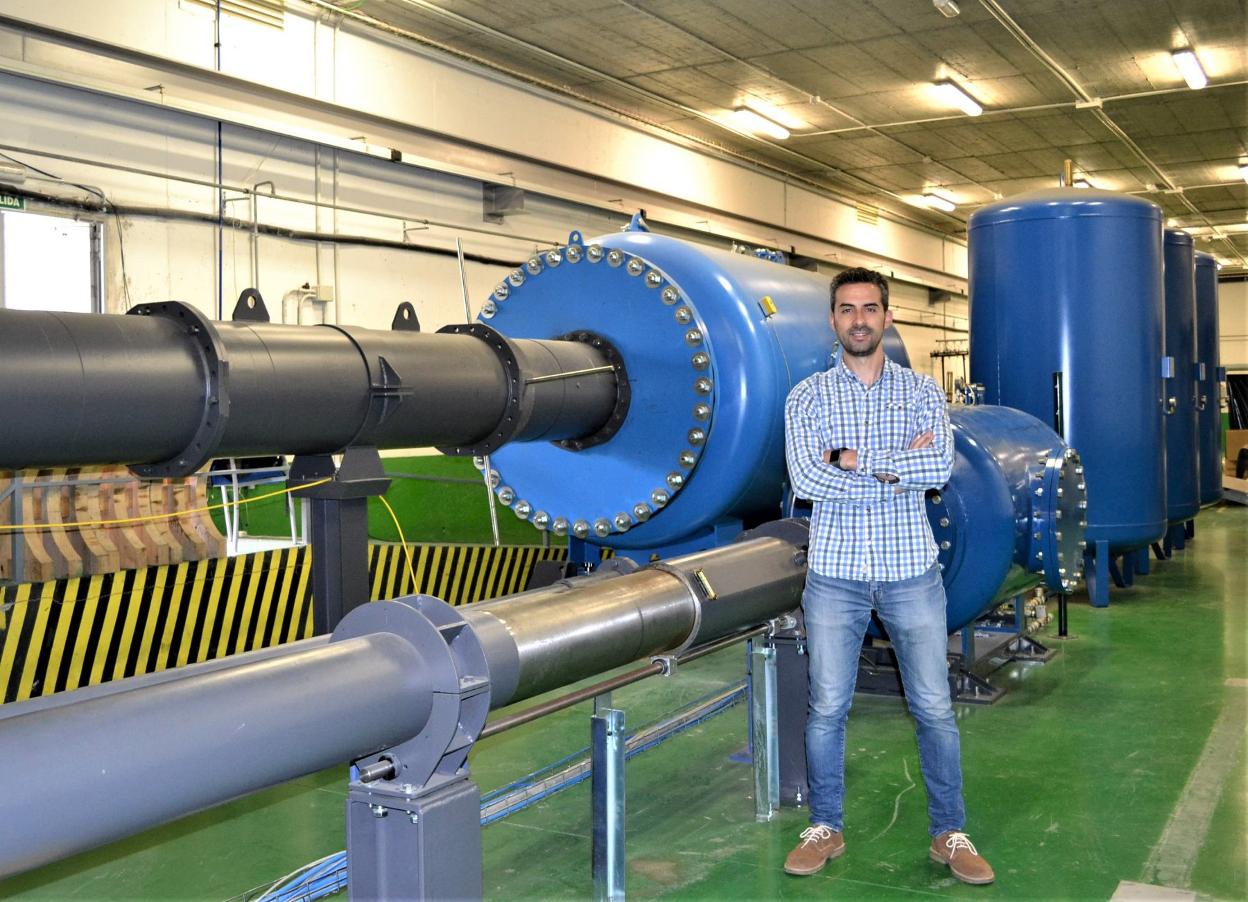
Secciones
Servicios
Destacamos
EUGENIA GARCÍA
GIJÓN.
Jueves, 13 de mayo 2021, 13:55
Durante más de tres meses preparó su propuesta de investigación. Fue una de las cuarenta que, entre cerca de mil solicitudes, pasaron el primer corte. Y mereció la pena: finalmente fue uno de los diez agraciados. El gijonés Juan Carlos Nieto Fuentes (nacido en ... 1985), egresado de la Escuela Politécnica de Ingeniería, acaba de recibir la beca CONEX-Plus, un programa de movilidad y formación de la Universidad Carlos III de Madrid cofinanciado por la Unión Europea dentro del marco de las acciones Marie Sklodowska-Curie (MSCA). «La verdad es que estoy muy contento. Son becas muy competitivas y, pese al esfuerzo que conlleva solicitarlas, en la mayoría de los casos el resultado es negativo», manifestó en conversación con EL COMERCIO. «El Ministerio y las comunidades deberían pujar por retener el talento nacional y promover este tipo de becas de atracción de talento», reivindicó este egresado de la Escuela Politécnica que entre 2016 y 2019 hizo el doctorado en Mecánica de Materiales en el Instituto Tecnológico de Israel.
La beca, dotada con 200.000 euros, le permitirá continuar durante tres años con su investigación y seguir estudiando el comportamiento de materiales metálicos impresos con tecnologías 3D. «Estudiamos estos materiales para incorporarlos en estructuras resistentes y desmontar esa ideología de que al estar impresos en 3D son materiales frágiles que no se pueden usar en estructuras sometidas a grandes esfuerzos, como pueden ser las aeroespaciales, automovilísticas o de protección en el ámbito militar», detalló.
Lo que trata de demostrar el grupo de investigación encabezado por el profesor José Antonio Rodríguez Martínez. es que «la porosidad inherente a estos materiales impresos lleva a regularizar su comportamiento, de tal forma que se pueden llegar a utilizar en estructuras críticas» . ¿Cómo lo hacen? A través de un experimento denominado 'penetración axial de tubos a alta velocidad'. «En cañones de gas de alta presión introducimos un proyectil con forma troncocónica; cargamos el tanque con explosiones muy altas, de hasta cien bares, y se produce la aceleración del proyectil, consiguiendo hasta 400 metros por segundo de velocidad para apenas 150 gramos -señaló-. Cuando el proyectil sale del cañón penetra un tubo impreso en 3D con el material que queremos investigar, desde aleaciones de titanio, aluminio y magnesio o aceros inoxidables».
Una vez se produce el impacto, «estudiamos el tipo de fractura que se produce en los tubos, que tendrán distintos patrones en función del material, sus dimensiones geómetricas y porosidad». Todo ello lo trasladan al ordenador para «hacer simulaciones numéricas y estudiar el problema». El grupo está inmerso en otro proyecto con el US Air Force Research Laboratory.
¿Ya eres suscriptor/a? Inicia sesión
Publicidad
Publicidad
Te puede interesar
Publicidad
Publicidad
Nuestra selección
Esta funcionalidad es exclusiva para suscriptores.
Reporta un error en esta noticia
Comentar es una ventaja exclusiva para suscriptores
¿Ya eres suscriptor?
Inicia sesiónNecesitas ser suscriptor para poder votar.