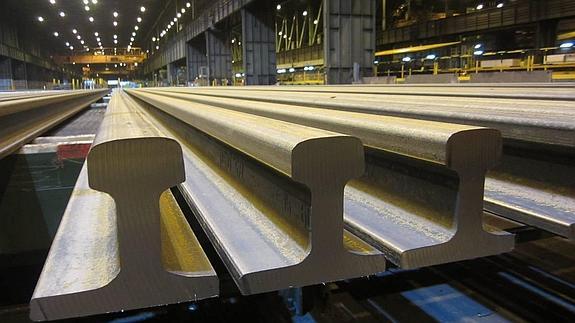
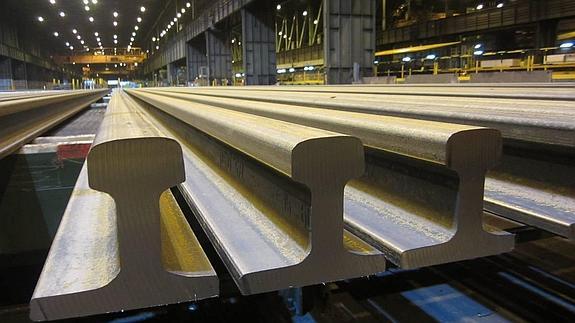
Secciones
Servicios
Destacamos
DIANA DE MIGUEL
Domingo, 25 de enero 2015, 00:42
El tren de carril de la factoría gijonesa de ArcelorMittal acaba de entrar en el exclusivo club de fabricantes de carriles asimétricos con cabeza endurecida, un selecto producto de elevado valor añadido que se utiliza fundamentalmente para los cambios de vía de los trazados ferroviarios. Ninguna planta del grupo siderúrgico fabricaba hasta ahora este tipo de carril por lo que toda la demanda mundial de este producto, que exige una alta precisión en su fabricación al contar con unas especificaciones técnicas muy concretas, se cubrirá desde Asturias.
El primer pedido salió de la factoría gijonesa el pasado mes de octubre y a lo largo de este mes está previsto que se expida un nuevo lote. Ambos fueron solicitados por fabricantes españoles de cambios de carril. El desarrollo de este nuevo tipo de carril se hizo íntegramente desde Asturias y requirió de varios meses de estudio. Según explican fuentes del entorno de Arcelor, hubo que empezar desde cero al emplearse un método de fabricación para endurecer la cabeza del carril mediante un enfriamiento controlado con chorros de agua, integrado en el tren de laminación, que es único en el mundo. Los dos fabricantes y grandes competidores mundiales de este tipo de carril hasta la fecha, Japón y Austria, utilizan respectivamente para el mismo fin aire comprimido y un polímero patentado.
En el proceso de fabricación de carriles de cabeza endurecida -el dispositivo se puso en marcha en 2012 en la planta de Gijón para carriles de hasta 72 metros en todas las normativas (Euronorma, Arema, UIC . ) y supuso una inversión de más de 25 millones de euros-, controlar la temperatura de enfriamiento es vital y si el carril es asimétrico, el proceso se complica aún más debido a la particular asimetría y geometría de los carriles y a la configuración de la refrigeración. La clave del proceso de endurecimiento está en enfriar en distintos grados y ritmos todas las partes del carril, de tal manera que se logra no solo una determinada dureza superficial, sino un mapa de durezas internas que permiten garantizar la resistencia de la pieza en las condiciones más exigentes.
Aunque la planta gijonesa de ArcelorMittal venía produciendo desde hace años carriles asimétricos, hasta ahora no podía producir esta nueva gama para cambios de vía, más específica, de cabeza endurecida lo que le había impedido optar a numerosos concursos de compra de carriles en los que se exige a los fabricantes producir todos los tipos de carriles para optar a su adjudicación. De ahí la trascendencia que para la compañía tiene haber incrementado su oferta de carriles, no tanto por el volumen de producción, que será pequeño, sino porque le permite diversificar su gama de productos siderúrgicos y llegar a nuevos mercados internos y , sobre todo, exteriores, dos de los principales objetivos que se ha marcado la planta asturiana.
El grupo ArcelorMittal cuenta con un total de tres centros de producción de carriles. Además de Gijón, la planta americana de Steelton, que produce carriles asimétricos pero no con cabeza endurecida, y las polacas de Dabrowa Gornicza y Krolewska. El carril es, por sí mismo, un producto siderúrgico de gran complejidad, tanto por los aspectos de diseño técnico y proceso de fabricación, como por el constante aumento del nivel de exigencia en las condiciones de servicio.
Debe ser capaz de dar respuesta satisfactoria al incremento de las cargas arrastradas, los aumentos de velocidad, la mayor frecuencia de paso, la comodidad (en las líneas de pasajeros) y, muy especialmente, a la seguridad vial. Son fundamentalmente los gobiernos los que demandan este tipo de carril.
La factoría de ArcelorMittal de Gijón comenzó a producir vías de alta velocidad en 1990, coincidiendo con el inicio del desarrollo de la red de alta velocidad en España, lo que le ha permitido adquirir una gran experiencia en este nicho de mercado, muy especializado.
Con más de un millón y medio de toneladas producidas hasta la fecha, los carriles de alta velocidad fabricados en Gijón están presentes en las infraestructuras de más de 30 países, como España, Francia, Portugal, Alemania, Turquía, Arabia Saudí y Marruecos.
El tren de carril de la factoría gijonesa está, por otro lado, pendiente de una importante inversión de en torno a 23 millones de euros para adecuar la instalación a la fabricación de un carril de 108 metros, frente a los 90 de la actualidad, que le permita llegar a nuevos mercados.
La inversión, que supondría una inyección de calado de cara a la modernización de las instalaciones de Largos, ya ha pasado una primera criba de la multinacional, pero todavía está bajo estudio. De ella depende que la compañía pueda incrementar su producción de Largos hasta el millón de toneladas en el horizonte de 2018, frente a las 790.000 de 2014. Un incremento productivo que supondría, además, elevar hasta los cinco millones de toneladas la producción de los hornos altos durante el periodo 2016-2018, de acuerdo con la planificación que maneja la empresa. En la actualidad, la producción de los hornos ronda los 4,4 millones por lo que supondría un aumento de en torno al 12%.
Publicidad
Publicidad
Te puede interesar
Publicidad
Publicidad
Esta funcionalidad es exclusiva para suscriptores.
Reporta un error en esta noticia
Comentar es una ventaja exclusiva para suscriptores
¿Ya eres suscriptor?
Inicia sesiónNecesitas ser suscriptor para poder votar.